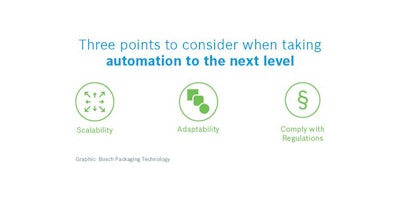
According to the Canadean intelligence database on the outlook of the biscuit market[1], China is the largest plain cookie and cracker market by volume, with a 63 percent projected market growth between 2014 and 2018, followed by India, with an expected growth of more than 103 percent. Latin America, Western Europe, South East Asia, North America and the Middle East and Africa also offer high growth rates of between 30 and 66 percent.
It is hard to meet such rapidly increasing market demands without fully or partly automated production lines, especially in developing markets where the share of manual processes is still high. Food manufacturers mirror this statement, naming investments in technology as the main source of significant cost rises (44 percent) up until 2021[2], followed by investments in innovation into new packaging types (43 percent) and complying with legislative changes (33 percent). At the same time, 29 percent of respondents expect to benefit from investment in manufacturing equipment over the next five years.
There are many perceived challenges relating to automation. When considering new equipment for their flexible packaging systems, European manufacturers prioritize running costs, while North American producers are concerned about the initial cost of purchase; Asia-Pacific companies are searching for ultimate adaptability to different pack sizes and materials, whereas the rest of the world opts for ease of operation[3] (see chart 1). Machine speed accounted for only eight percent of global manufacturers’ concerns.
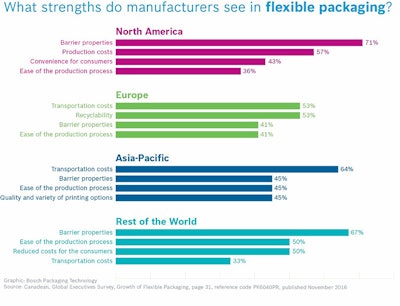
At Bosch Packaging Technology, we discussed automation issues extensively with our biscuit customers and prospects. There are three main areas of concern when taking automation to the next level (see chart 2):
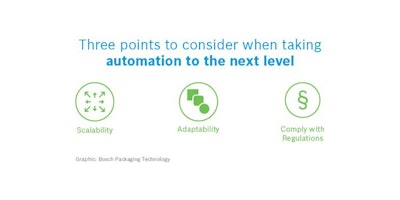
Scalability is the first stumbling point. For biscuit manufacturers automating for the first time, or testing new products and markets, fully automated lines might be too high a barrier for entry. New companies may start with hand-fed wrappers for cookies and crackers, gradually adding feeding systems, carton erectors and formers.
The easiest way to start is to have manual secondary and tertiary equipment with automated primary packaging at the heart of biscuit packaging. All other elements can be automated at a later stage, allowing producers to grow their production in line with sales (see chart 3).
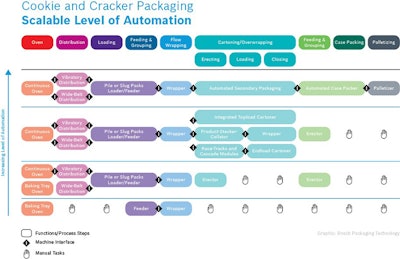
Adaptability to various pack sizes, formats and materials is the second important point of concern. For some manufacturers in emerging markets, the ability to reduce or increase the number of biscuits per pack, if required, is a matter of survival against fluctuating raw material costs. For others, an opportunity to run seasonal promotions and adjust to consumer demands is an important factor. All of them, however, are looking to future-proof their production.
Biscuit producers need to consider how easily they can change between different pack sizes and formats. For example, when designing a packaging system, conventional magazine feeders limit the number of biscuits per stack to the number of incoming lanes, or a multiple of this number. The reason behind this, is that typically only a fixed amount of biscuits could be extracted per magazine. To create a stack of eight, either eight magazines would be required, or four if two were extracted at once. To create a stack height that is different from the amount of magazines or its multiple, major changes to the packaging system would be required, such as implementing additional vibratory channels.
Innovative technologies, however, allow for format flexibility independent from incoming product supply, enabling manufacturers to change the stack height as well as pack configuration without alterations of the production line. Product shelf differentiation is boosted thanks to the high variety of options tailored for diverse demands of targeted customer segments. At the same time, primary packaging can now be easily adapted to various secondary and end-of-line packaging needs, whether this be retail-ready sets favored by supermarkets or sales units ideal for the weekly family biscuit supply.
Easy changeovers allow producers to reduce operator errors and downtime through repeatable and programmable set-ups. Tool-less changeovers should always be the preferred choice for manufacturers, especially in regions suffering from a lack of qualified personnel. Innovative “push-button” changeovers, for example, enable biscuit stack height changes via programmable modifications to recipes.
Compliance with legislative changes is the third most important concern for manufacturers, as they face increasing pressure to enhance safety in the food supply chain due to new global regulations. This includes the final rule of the Food Safety Modernization Act (FSMA) published in September 2015. Compliance became mandatory for companies with less than 500 employees in September 2017, with the final deadline for smaller manufacturers (with annual revenue below $500,000) in September 2018. Packaging machinery manufacturers work closely with food producers to ensure that equipment complies with the latest regulatory standards.
Automating production lines makes it easier for biscuit producers to meet specific hygienic requirements by, for example, limiting human contact with the product. Other areas to look for include easy-to-clean features, accessibility and open machine design. Fewer cables, crevices and holes that can trap food ensure systems are not only sanitary but also easy to maintain, boosting uptime and therefore productivity.
About the author
With more than 10 years of working at various roles at Bosch Packaging Technology, Andreas Schildknecht combines a deep understanding of the packaging world with passion towards strategic management. After acquiring his MSc in strategy, technology and management from Danube University Krems, Austria, Andreas held positions in the pharmaceutical team and was in charge of the global product management for the horizontal for, fill and seal (HFFS) solutions. Currently he is responsible for the strategic development of mid-range system solutions for Bosch Packaging Food.
[1] Source: Canadean intelligence database, Biscuit-Outlook_Countries_Value-Volume_2014-2018, Category includes Cookies (Sweet Biscuits) and Savory Biscuits_All sub categories, 21.09.2015 10:04:29
[2] Source: Canadean Report; Opportunities and Threats to the Packaging Industry in 2021, Page 12, Reference Code: PK 6010PR, April 2016
[3] Source: Canadean, Global Executives Survey, Growth of Flexible Packaging, page 40-41, Reference code PK6040PR, published November 2016