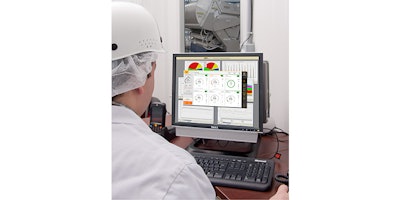
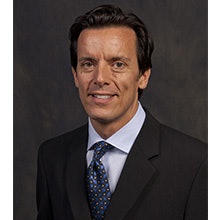
With the world’s population expanding at a rate of more than one percent a year and urbanization trends increasing the demand for convenience foods, we’ll need to double our global processed food output over the next several decades just to keep pace. That means the food supply chain, from the grower to the retailer, must continue to improve efficiencies, reduce waste and increase yield. At the same time, we’re tasked with improving food safety and product quality to comply with new regulations and meet consumers’ rising expectations. Visionary thought leaders are searching for solutions to these challenges.
In this article, I will explore how digital data is starting to transform food processing operations and the food supply chain at large. The benefit for early adopters is the creation of competitive advantages that come from improved efficiencies and tighter control over product quality.
The Supply Chain
At each step within the supply chain, leveraging advanced sensor technologies and smart systems to collect, analyze and share digital data, for the purpose of turning that data into actionable knowledge, promises to improve operations.
Growers already monitor field and environmental conditions to better manage pests, adjust nutrients and schedule planting and harvesting in order to produce larger and higher quality crops. Food storage facilities audit temperatures and humidity to more accurately manage storage conditions and reduce spoilage, maximizing food safety and product quality. Food processors and packers, for their part, have an increasing opportunity to leverage smart technologies at multiple points within their operations to improve production efficiencies, food safety, product quality and process yield. Distributors automate track-and-trace to reduce inventory and better secure their portion of the supply chain. Finally, retailers can identify changing consumer preferences in real-time and more quickly adjust their product offerings to reduce waste and improve profitability.
Now, imagine the Industrial Internet of Things (IIoT) takes the data collected at each step of this supply chain to the cloud and creates an integrated end-to-end information exchange from farm to fork. A digital sorter at a food processing plant may be collecting data about the color, size, shape, structural properties and chemical composition of every object at raw product receiving. That data can be shared with the grower, for example, informing them their cranberries are too white or yellow, so they know to add sulfur to their crops earlier in the season next year to improve quality. Or fruit packers with the ability to measure natural sugar content in their product can accurately direct specific product batches to specific regional markets, based on consumer preference for a sweeter or tart taste profile.
To take a page from the track-and-trace initiatives now being embraced by pharmaceutical manufacturers — serialization and aggregation solutions could be adopted by those in the food chain to offer greater transparency and security. Such efforts would help industry players respond more quickly to food safety and product quality problems, allowing them to speed resolution and promptly isolate the problem to limit exposure.
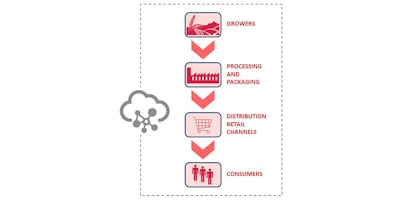
Food Processing
While the vision of integrating the entire supply chain is futuristic, the digital data revolution is well underway at many forward-leaning food processing companies, with a multitude of benefits that depend on the nature and extent of adoption.
Data from a smart machine can improve its own operations, performing self-diagnostics, sending smart alarms and performing auto-learning functions, among other things. Integrating equipment on a line enables digital data from one system, sensor or line-control device to improve other systems along the same production line. Delivering data to the enterprise level empowers the large-scale analysis of ‘big data.’ Whether the data is collected manually on the plant floor or remotely via a connection to the factory’s MES or SCADA system, in batch-mode or real-time, processors that collect, analyze and share larger volumes of digital data can make more informed decisions. Turning data into knowledge through intelligent analysis, a food processor can ultimately help protect food safety, optimize product quality, improve production efficiencies and reduce operating costs.
Tapping Digital Sorters
Digital sorters, which serve the primary purpose of removing defective products and foreign material from a food processing line, are ideally suited to contribute to the digital data revolution. Sorters inspect 100 percent of the product on the line, recognizing each object’s color, size, shape, structural properties and/or chemical composition, depending on the sorter’s sensors and software. Today’s advanced sorters feature powerful computers that can process increasingly large volumes of data. When equipped with "information analytics" capabilities, they can collect real-time data and generate reports about the sorting process and every product and object flowing through it, whether that data is used to make sorting decisions or not.
Around the world, leading food processors are demonstrating how to mine data from their digital sorters to improve their operations. Because this capability is thoroughly customizable, there are almost as many examples as there are food processors.
A sorter inspecting raw product at receiving can analyze the quality of incoming product by lot or by supplier, enabling the processor to develop a payment scheme that rewards higher quality. A sorter located after a transformational process can collect data used to control that upstream process. For example, a whole potato sorter can detect remaining peel and control the upstream peeler in real time to increase or decrease dwell time. Or it can offer predictive analysis, sending a smart alarm as soon as certain conditions of interest begin trending in a problematic direction. At the end of the processing line, immediately prior to packaging, a sorter will ensure the product is free of contaminants and can collect valuable data about final product quality to help control upstream processes and strengthen record-keeping. For processors that have multiple sorters, data can be compared, either before and after a transformational process or one line to another or one facility to another, offering new levels of insight to help managers optimize their operations..
Conclusion
Given how the digital data revolution is already transforming food processing plants, it’s easy to imagine a new set of possibilities, particularly as the trend extends to the entire food supply chain. Leading food processors are collecting, analyzing and sharing digital data across their enterprise to better maintain food safety, optimize product quality, improve production efficiencies, increase yields and reduce operating costs. Others in the supply chain, from growers to distributors and retailers, are also leveraging digital data based on their requirements to improve their operations.
The next wave will come from fuller data integration throughout the food supply chain, from the field to the consumer’s plate, with each constituent collaborating to share information seamlessly beyond the walls of their entity to benefit the overall process. The technology exists and the industry needs it to achieve its growth objectives.