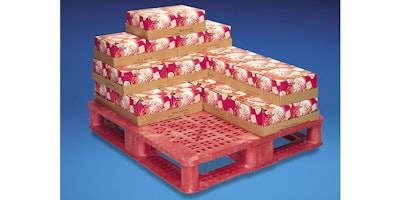
Regulation changes and the sophisticated understanding consumers have about food safety have created a need for pallets that help minimize the chances of contamination and poor handling, which are closely tracked in today’s food supply chains. These consumer concerns and industry standards have motivated companies to re-evaluate their systems and the materials that come in contact with goods.
To ensure consumers are exposed to foods and beverages that were handled with care during storage, transportation and warehousing, pallets that reduce the chances of unsanitary contact are essential. Plastic pallets — specifically hygienic pallets — have the characteristics that make them highly suitable for the food and beverage industry.
So, knowing they are needed, what about them is worth a system upgrade? Below is a guide to choosing the appropriate pallet that can withstand a quickly evolving industry.
Hygienic Pallet Characteristics
Hygienic plastic pallets first hit the market more than 25 years ago. In a short amount of time, these pallets have been refined to better serve food processing plants. They are typically based on the standard 40” x 48” footprint for efficient use of warehouse space. Pallet features have improved to become more practical, safe and sanitary. Hygienic plastic pallets were first used in the pharmaceutical industry, as there was a strong demand for pallets that handled high-value pharmaceutical products with the utmost care and security. This trend extended into the food and beverage industry when food safety awareness started growing.
Since then, hygienic pallets have become an essential piece of the supply chain for food and beverage companies looking to gain and keep public trust. Their characteristics make them reliable and long-lasting. They are easy to sanitize, as the non-porous platforms are designed to support sanitary conditions and keep equipment clean. The one-piece, cavity-free body leaves few areas for contaminants to collect. The open deck allows airflow so the pallets are easy to clean and fast-drying. The contoured surfaces and corners lower the risk of product damage due to punctures or snags. Lastly, hygienic pallets do not rust, have nails or staples, lose boards or absorb moisture and odor.
Many of these features are non-existent or hard to find in plastic pallet alternatives, such as wood, metal or fiber corrugated. Even though wood pallets are still widely used today, many plants are making the switch to plastic. In fact, 38 percent of pallet users are turning to plastic because of the durability and reusability.
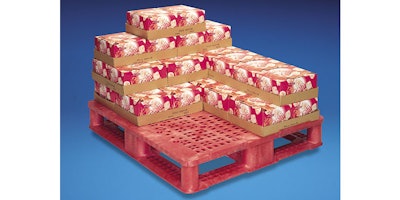
The Reason for Plastic
Pallets are a top checklist item because of their constant contact with products and equipment — the pallet material is a determinant in the safety improvements companies make. A main factor for new material handling and supply chain considerations is the Food Safety Modernization Act (FSMA). Implemented in 2011, FSMA has caused companies that deal with food and beverage handling to re-evaluate their processes and overall systems.
Leading food processors and their suppliers are considering plastic for their pallet material to abide by the new requirements set by FSMA. Plastic allows for easy cleaning, allergen management, detectability, color coding, labeling and radio-frequency identification tags. In addition, the material doesn’t retain moisture and withstands a wide temperature range. The following are characteristic of plastic hygienic pallets:
- One-piece, cavity-free design
- 100 percent virgin resin content, meeting the FDA’s requirements for an approved material for direct food contact
- Prevents absorption of environmental contaminants like odors, bacteria, pesticides, etc.
- Allows for high-temperature washing
- Flow through design, regardless of pallet orientation
- Can be X-ray or metal detectable
- Custom colored to color code and segregate loads
Wood pallets cannot meet many of these factors because of the material’s inherent ability to absorb and retain surrounding elements. Wood pallets are often shared or repurposed, so it is hard to know what has permeated into them. Because wood pallets cannot be sanitized, unwanted elements cannot be eliminated or washed off. Wood pallets can break easily, which increases the chances of broken and often unsafe wood pieces on the plant floor.
Unlike wood, plastic provides the consistency needed for proper equipment, storage and transportation use. They are precisely molded and dimensionally consistent, for a repeatable performance with equipment — this ensures a precise truckload, proper fitting of totes and accurate interfacing with robotic and automated equipment. Each wood pallet, on the other hand, has a different size, look and feel.
Embarking on the Transition to Plastic
Any type of change in material handling practices can create a need for facility updates. It is now recommended to design supply chain systems around the pallets. Knowing the pallet material and design upfront ensures compatibility with automated plant equipment, such as tracking and conveyor systems. This is why the entire system must be analyzed when considering a new pallet. A reconfiguration of this importance will be beneficial in the long run, because, like many others, the food industry is known for new product launches, new case sizes and updates to its best practices and regulations.
In addition, plastic pallets have the ability to adapt to continuous change. Not only do they have a longer service life, but they also can adjust to new needs, such as upgraded automated and material handling equipment, labor practices, production process and material flow to ultimately satisfy customers and consumers. If more assistance is needed in choosing the pallet that best fits your needs, follow this five-step selection process.
- Analyze: Review the product’s life cycle. Identify product load characteristics (boxes/cases, powder, liquid), temperature requirements, dimensions, weight, value and load distribution. The level of cleanliness also should be determined.
- Select/design: Determine the required footprint and pallet style, including rackable, stackable and nestable.
- Justify: Compare annual pallet costs, environmental impacts of the alternatives and the characteristics of hygienic pallets.
- Implement: Be sure all of the stakeholders are engaged (operations, material handling, maintenance, etc.) to conduct a small trial. Afterward, be sure all employees are trained on how to use the pallets and each of the features.
- Evolve/continuous implement: Do not stop exploring other materials because, as mentioned above, plants will not stop expanding the use of pallets, and new technologies and equipment will evolve to work more efficiently with them. This is why the right material is important in the long run.
For the complete hygienic solution, consider additional material handling products that work with plastic hygienic pallets for a complete reusable, sanitary material handling system. There are a variety of plastic totes, such as ventilated totes, that stack and nest together when placed on pallets. As in the name, they are ventilated for easy cleaning and fast drying. Top caps can be placed on top of the totes to create a stable unit load for pallets. They keep dust and debris away from the exposed goods in the totes. They also nest with one-piece hygienic pallets to secure stacked loads and increase worker safety. The top cap, tote and hygienic pallet combination is the full package.
The Future of Plastic Packaging
Plastic packaging has become a popular consideration with the customizability, consistency, benefits and longevity it brings to supply chains. One day, supply chains may consist entirely of plastic packaging as new designs are created and the need for faster adaption becomes mainstream. For now, hygienic pallets should be considered for food and beverage supply chains because the features closely correlate to the requirements under FSMA, which increase the trust of customers and the health of consumers.