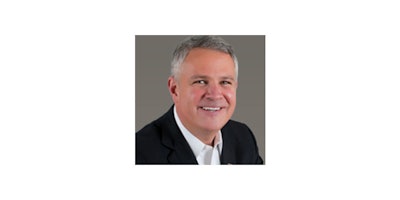
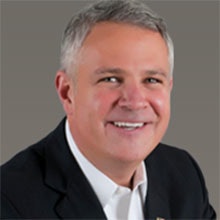
This year more than ever, food manufacturers are operating in an increasingly volatile environment and are subject to ingredient shortages, food safety demands and rising prices. Maximizing efficiency is both a constant and pressing need. In 2016, we saw a growing number of food manufacturers focus on implementing efficient and cost effective processes that overcome these challenges and ensure long-term profitability. In many ways, manufacturers have taken it back to the basics. Let’s look at some back-to-basics process innovations that were widely adopted in 2016 and will continue to impact F&B manufacturers in the years to come.
Product Optimization
Whether it’s minimizing product that is lost in the line clearance process during product changeover, or reducing overuse of core ingredients in an attempt to ensure products meet nutrition labels, food manufacturers are optimizing processes to minimize waste of product.
All F&B manufacturing processes have the risk of generating excess waste. Lean Six Sigma and statistical process controls continue to help manufacturers better manage things like ingredient use, line changeover product usage and packaging overfill. They’re seeing the potential that optimizing ingredients and finished products has for giving them a competitive advantage and bringing substantial savings, without added capital investment.
For companies that have not yet engaged in optimization and maximization of use of critical raw materials, they will likely do so in 2017 as food prices, availability and other factors increase costs and volatility. Generally speaking, product optimization efforts are not difficult to pursue, but the challenge resides in putting the initial processes in place and then capturing, reviewing, and using data on a consistent basis for results. Optimization efforts should begin with capturing and analyzing data so that targets can be adjusted as necessary. Manufacturers that have been successful with this establish meetings and cross-functional teams to implement goals and measure results.
Zero-Based Budgeting
Today, we operate in an industry where every penny counts, which is one reason 2016 brought a rise in zero-based budgeting (ZBB). Unlike incremental budgeting, where last year’s budget serves as the primary driver for budget allocations in the coming year, ZBB allocates funds based on the merits of each department’s policies, goals and spending justifications.
Once spurned due to its long, resource-intensive planning process, ZBB is gaining momentum among F&B manufacturers that champion accountability, metrics-driven decision-making and performance/results. According to a report from McKinsey and Company, there was a dramatic increase in the use of ZBB among the largest corporations in the United States: from 14 to 90 between 2011 and 2015.[i]
With zero-based budgeting, all budgetary allocations for the financial year are set at zero. Departments seeking financial allocations for the coming year must then present complete data justifying their projected expenditures. The result is a careful review and analysis of each and every item on which money is spent, something that fails to occur in most businesses.
Whether driven by new leadership, a turnaround effort to improve financial performance or a way to drive positive cash flow and profitability, ZBB is driving lower expenses, better knowledge and results-oriented management in the companies that pursue it.
For manufacturers that are dissatisfied with their current budgeting procedures because they feel they are inadequately allocating funds or those who feel that programs funded are not aligned with company goals, ZBB can provide more visibility and control, and put discipline around departmental budgeting and spending. Others may have attempted to implement ZBB with lackluster results, often attributed to poor or partial implementation. These companies can learn from their experiences and, with a little help, re-implement ZBB with full success.
KPI-Driven Decisions
The days of “gut-feel” and relationship-based decisions are over. Companies have access to the information for making objective, data-driven decisions. Yet still, many have had to undergo significant culture changes to truly begin using that data to drive business decisions. The most forward-thinking F&B manufacturers are striving to transform their culture from one of “gut decision-making” into one that bases decisions on facts and information.
Leading manufacturers are injecting new “DNA” into the operation, systematically countering employees’ natural tendency to lose focus on the facts and bypass rational decision-making, and aligning thought processes and work behaviors much more closely with rational ideals of how the business should operate. The most effective operating systems are comprised of plans, targets, KPIs, reports and cross-functional review forums that ensure employees use valid data to identify and impact the root causes of overall performance. The manufacturers that have accomplished this have seen results that are beyond impressive, generating annual savings in the tens of millions of dollars while also building a long-term, sustainable competitive advantage
Looking to 2017
With so many technology advancements and solutions on the market, it is easy to become distracted with the “latest, greatest” capabilities. However, doing so at expense of ensuring the fundamentals are in place can be a mistake. Are you leveraging the basics to stem the tide of increased cost and to truly maximize the resources you have?
About the Author
Doug Newman is a partner with Myrtle Consulting and is responsible for business growth and development. In his more than 20 years of experience in manufacturing and consulting, Doug has developed a unique combination of experience that makes him a resourceful and creative problem solver with the vision and communication skills to formulate enterprise based solutions. For more information, visit https://www.myrtlegroup.com.
[i] Matt Fitzpatrick and Kyle Hawke. “The return of zero-based budgeting.” McKinsey and Company. August 2015. Web 8 Dec. 2015. http://www.mckinsey.com/insights/corporate_finance/the_return_of_zero-base_budgeting