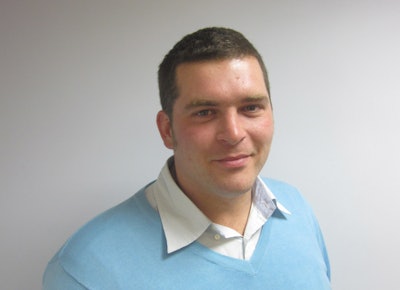
City Technology discusses emissions gas monitoring applications and how the right sensor can improve accuracy and reduce service costs
What do the gases flue gas analysers detect and why is detection important?
The main products of incomplete combustion are usually CO2, CO, H2 & NO; to ensure safe combustion we measure CO and the remaining O2 after combustion to calculate a CO:CO2 ratio – the accepted benchmark of performance. Of course there is much more to understand regarding efficiency or environmental emissions. CO sensors are also sensitive to H2 so in our more demanding markets, we measure the H2 to compensate the CO reading.
The combustion process is complex, requiring the right mix ratio, turbulence, temperature and time for reactants to combine. Poor fuel mixing or too little air produces carbon monoxide (CO) and soot. If the flame temperature is too high, nitric oxide (NO) and nitrogen dioxide (NO2) are produced. A fuel containing sulphur will produce sulphur dioxide (SO2) - all these gases are toxic and indicate inefficient combustion, which is both dangerous and costly in terms of fuel consumption. Oxygen (O2) is essential for combustion so the gases detected by a typical flue gas analyzer are O2, CO, H2, CO2, NO, NO2, SO2 & H2S.
Why is the choice of gas sensor so important?
There is a lot of focus on the analyzer specification itself, but it’s also important to remember that an analyzer is only as effective as the sensors it uses. Because of the risks associated with combustion emissions, safety and reliability are critical. Due to the nature of the typical toxic gas sensor used in a flue gas analyzer, emissions gases and products of combustion can produce cross-sensitivity issues.
Field failures can be dangerous and costly and lives depend on a good sensing technology. What is less widely recognized are the other economic benefits a gas sensor can bring, by reducing an analyzer’s servicing needs and operational costs.
In a real-world context, a combustion check can take up to 15 minutes and is typically carried out up to 8 times in each working day. With improved response times, new sensors can allow the same combustion check to be carried out in half the time or less. This means much less time waiting for the reading to stabilize – and ultimately a valuable opportunity to carry our more services in the field. Faster response is what engineers really value as they have to wait less time for the reading to stabilize which can lead to more accurate readings as they are less likely to take the reading too quickly.
You mention adverse conditions that can affect sensor performance – what are these and how do benchmark sensors overcome such problems?
Flue gas analysis in domestic and light commercial boilers can present a challenge for sensors because they are subjected to high humidity, temperature and pressure changes, corrosive and acidic gases, and cross-sensitivity from emissions gases. This can cause field failures, compromise sensor integrity and create considerable servicing needs.
Every component in a sensor should be built to a high specification using ultra resistant materials, so they can work effectively in these adverse conditions without affecting accuracy and reliability and deliver the fast response times. Sensor design is essential in achieving this. Our long life oxygen sensors are built using “electrochemical pump” technology which is proven in the field for 4 years and provides a viable lead fee replacement.
A high range CO monitoring application, which traditionally requires a second sensor under EN50379-2, benefits from the use of a robust, high sensitivity solution like our new A5F+ CO sensor, which can monitor up to 20,000ppm. The combination of high capacity filtration to remove SOx and NOx and auxiliary electrodes to compensate for hydrogen, provides the highest reliability.
What should an analyser manufacturer or engineer look for when selecting a sensor manufacturer?
It’s important to work with a manufacturer who is a recognized expert in the field of emissions monitoring. The ability for a manufacturer to achieve dependable repeatability should also be a key consideration. At City we use Six Sigma driven design, state-of-the-art automated manufacture and pioneering cell design innovations. Not to mention compliance with the latest standards. Our new 4 Series range is designed to meet the needs of EN50379-3 compliant analysers and features a long life solutions.
How does the right manufacturer back up such claims?
Marketing claims must be substantiated. Ask to see comparisons that back up “best in class” claims. Data speaks for itself - a good manufacturer will be keen to show you how their products shape up to contemporaries.
When it comes to reliable performance stability, testing – both life cycle and field tests – provides the peace of mind that a sensor really is up to the job of emissions monitoring. Always ask to see test data that can prove that what a sensor claims it can do is accurate. At City, extensive testing is an integral part of the design process, highlighting performance and sensor robustness. The measure of how good we are is how consistent our sensors are when they get to our customers.
Tom Gurd has worked for City Technology for the past 10 years as a Product Manager, specializing in emissions, environmental and industrial safety gas sensing. With a BEng (Honors) Degree in Mechanical Engineering, Tom spent the early part of his career designing and developing military and aviation products. Since joining City Technology in 2004, Tom has developed a wide ranging expertise in the field of gas sensing. Combustion analysis products developed by City Technology help to reduce pollution and save the lives of thousands of people every year. www.citytech.com