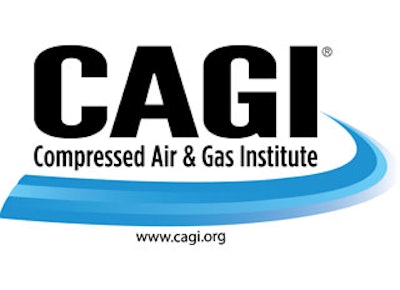
Mechanical equipment typically comprises 30% of the total capital investment in a new plant project. LSTK (lump sum turnkey) projects involving a contractor will focus on capital, installation and commissioning costs. The āafter startupā costs, such as power consumption, maintenance, on-stream time, spare parts consumption and others, may not always receive equal consideration in equipment selection. The end user may not be getting the best value over the life of the plant, as a result.
There are several parameters that make up a complete mechanical equipment life-cycle cost evaluation, including how to determine what is most critical for a given project. It is essential to discuss some of the less frequently considered elements, such as performance, reliability and maintenance costs, as well as design flexibility, future growth and cost of doing business.
There are many factors that can affect the total life-cycle cost (sometimes referred to as ātotal cost of ownershipā) of mechanical equipment. Each of these factors should be considered when evaluating bids for new or refurbished equipment installations. Suppliers work to offer the lowest possible life-cycle cost, based on the capabilities of their equipment (see inserted life-cycle chart).
Equipment Purchase Cost
First entry on a bid evaluation is the purchase price. The following factors contribute to the ātotalā equipment purchase price. Scope of Supply: scope will typically follow customer specifications. The review of scope requirements should include the supplier, contractor and end user customer. Comments and exceptions are to be addressed. Accessories quoted, such as drivers, dryers, filters, valves and instrumentation should be evaluated and ratings of each noted. The impact of differences should be included in the evaluation, such as redundancy, excessive margins on capacity, power or design pressures, upgraded materials of construction, customized versus supplier standard design and non-standard testing. Careful analysis of options is important in selecting and efficient and reliable system at the lowest initial cost. Over specifying or under specifying are common mistakes.
Freight
A lot of variations to freight terms, but one as simple as FOB job site, can be the most practical and least expensive for all parties.
Installation Costs
The impact of installation costs should receive due consideration. The evaluation may use delta costs as opposed to total actual costs, for equipment of similar design.
Complexity of Installation
The size, type, configuration and extent of packaging, all impact the installation cost. Additionally, field assembly may be required for larger units, including installation of maintenance accessibility platforms, foundations and grouting. Large equipment components may require mounting on a concrete pedestal, using soleplates, rather than on a base plate. Other factors that can affect installation cost include field assembly of main equipment, separately installed accessories, interconnecting piping and wiring, crane capacity and supplier supervision. The cost of a building to house equipment, including building permits, internal maintenance, crane costs, heating, cooling, insulation, must be included if applicable. Noise levels and costs to provide noise abatement, may affect the decision to provide a building.
Field Service / Training
Cost of technical assistance should be included in the evaluation. This can include installation and commissioning. Service cost can be lump sum or per company service schedule rates. Training can be onsite or at manufacturing plant.
Spare Parts
These can include installation and start-up spares, plus maintenance parts for normal operation and major capital spares. Major capital spares determined by end user customer, based on location, access to parts, lead time of parts and amount of acceptable downtime of equipment and facility.
Delivery Schedule
The delivery schedule for some projects can become a critical issue. Cash flow models should be developed to determine the economic impacts to adjust the delivery schedule to meet the construction need date. Sometimes delivery of drawings and documentation is more important than the equipment delivery. Sometimes storage costs are required when the site is not ready to receive the compressor(s).
Energy Costs
Energy cost is one of the largest components of total life cycle cost. It is important to understand the complete performance profile, such as guaranteed operating point, turndown points, air properties and ambient conditions. Startup and shutdown conditions should also be considered.
Flow Rate
Specified flow rate is an important factor in the evaluation process and should match specifications. Air compressors will have a standard delivered flow rate to the process. The specification or end user customer / contractor, should define the basis for the delivered flow rate. Other standards can be used as long as the basis is defined.
Evaluated Power Costs
Shaft power, typically expressed in brake horsepower (BHP) or shaft kilowatts (SKW), equals the sum of air horsepower, mechanical losses and convection losses, in rotating equipment. The parameters defining the cost of energy and the operating points to be evaluated, should be defined in the inquiry documents so the suppliers can optimize their equipment selection.
There are several types of performance guarantees and these should be defined in specifications or by end user, customer, or contractor. The guarantee basis usually includes a tolerance on the performance parameters. Centrifugal compressors can include tolerances.
Other Utility Costs
Life-cycle cost analysis should consider other factors such as external air or gas requirements for purging or sealing, instrument air, coolant and power consumed by auxiliary system.
Flexibility / Future Growth
The range within a compressor frame or model of a centrifugal compressor has the capacity to produce more or less flow and can be a consideration if future requirements are known.
Reliability
End users will generally require the equipment to operate for long periods of time without being shut down for maintenance.
Maintenance
All equipment requires periodic maintenance to ensure reliability and optimum performance. Comparison of recommended service and parts schedule is needed. Further consideration should be given to the financial impact of in sourcing service versus supplier service contracts.
Cost of Doing Business
The total life-cycle cost evaluation should include the relative cost of doing business. Factors that may affect this are the following: design coordination, timeliness and accuracy of supplier documentation, quality assurance and inspection, expediting, travel costs, pre-negotiated commercial terms. Alliances, partnering, development of standard designs / specifications and well established working relationships can all minimize the relative cost of doing business.
Integrally geared, three-stage centrifugal compressor technology yields lower specific power, BHP/100, compared to two-stage compressors. Life-cycle costs evaluations should always include these kW savings, elimination of replacement stage elements and higher annual maintenance costs.
The engineering contractor along with the end user may be able to justify increased capital cost if overall life-cycle cost savings can be demonstrated. Low price is not always low cost. The primary focus of a successful project team or organization is to add value for their customer. Communication between the end user, contractor and supplier, is of prime importance. Ask questions ā all questions are considered important when evaluating capital expenditures to support project economic goals.
For more detailed information on the centrifugal compressor technology or answers to any compressed air questions, please contact the Compressed Air and Gas Institute. The Compressed Air and Gas Institute is the united voice of the compressed air industry, serving as the unbiased authority on technical, educational, promotional, and other matters that affect the compressed air and gas equipment suppliers and their customers. CAGI educational resources include e-learning coursework on the SmartSite, selection guides, videos and the Compressed Air & Gas Handbook. For more information, visit the CAGI web site at www.cagi.org.