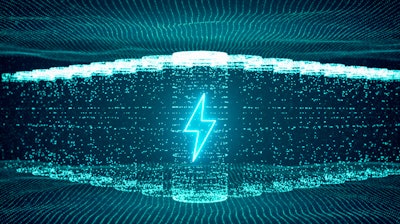
China dominates the global lithium-ion battery industry.
According to Benchmark Mineral Intelligence, China accounted for 75.3 percent of battery capacity in 2020, compared to 7.6 percent in Europe and 6.7 percent in North America. The West is gaining ground however. By 2030, the same analysts estimate that China will account for 65.4 percent of battery capacity, compared to 11.9 percent in North America and 19 percent in Europe.
This trendline is positive. The West is picking up the gauntlet and making headway in battery cell production capacity to supply the bourgeoning electric vehicle industry. These developments are necessary.
Combined, North America and Europe saw electric vehicle sales reach 2.1 million units in 2021 - through September, compared to 1.9 million units in China. Merely building out cell manufacturing capacity, however, is not sufficient.
China’s Dominant Position
Imagine two rooms separated by a door. One room contains minerals extraction while the other room houses battery cell manufacturing. China has the key to that door. Before extracted minerals can be used in battery cell manufacturing, they have to be refined to battery grade materials used in the manufacturing of precursor materials.
China controls more than 80 percent of cathode materials processing capacity for all critical elements, including cobalt, nickel, and manganese. The situation is similar in anodes. For example, analysts point out that 100 percent of all natural graphite anode is made in China.
China, meanwhile, only extracts 23 percent of global supply of all battery raw materials, according to Benchmark Mineral Intelligence. While Western governments are actively promoting electric vehicle sales and battery cell manufacturing, without a proportional investment to expand battery materials processing capacity, the reliance on China will not change one bit. This presents geopolitical and strategic risks that industry and government must consider.
Relying on China is Risky
The COVID-19 pandemic highlighted the potential dangers of long supply chains. The most well-known shortage resulting from global sea freight disruptions was microchips, which made it more difficult and costly to manufacture any product containing an electronic device, including electric vehicles.
While not as well known, battery cell production has been similarly affected by freight disruption. Then there is the geopolitical angle, best exemplified by the ongoing competitive dynamics in the rare earths industry, where China holds a dominant position and can open and close the door at will.
Localized, integrated battery supply chains offer quantifiable benefits. Shortened supply chains benefit the electric vehicle and battery cell industries in several ways.
- Reduced sea freight emissions: If we compare the ‘standard’ cobalt route, from mine in the Democratic Republic of Congo to cell in North America, for example, a North American primary refining and precursor industry would reduce sea freight emissions by at least 50 percent. If the same example is applied to Europe, emissions would be cut by 33 percent.
- Lower processing emissions: Chinese battery materials processing capacity is principally thermal coal-based. In North America, and Canada in particular, material processors have access to an abundance of clean hydroelectric power. As the industry is on the cusp of building out the North American battery supply chain from scratch, this industry-wide initiative is a great opportunity to ensure that we base it on hydroelectricity and renewables in its entirety, thus creating the world’s lowest carbon battery supply chain.
- Time is money. Shipping raw materials from North America to China, for these to return to North America in purified form is time consuming and expensive. The capital tied up in the existing supply chain is better spent on developing a local, integrated North American battery industry.
- Less material quality deterioration. The elemental properties of battery grade sulfates, for example, do not change dramatically over time. But physical properties do change, and material which is stored over longer periods risk caking and liquefaction. This makes handling more difficult. Shorter, local supply chains will ensure that superior quality material is delivered throughout.
- Increased transparency. In terms of material origin, China is not a global leader when it comes to transparency. It is difficult to ensure the ESG credentials applied to the material, which is shipped into China, also applies to the material which is shipped out of China. ‘Grey’ material – for example cobalt mined by children – may be mixed into a Chinese processing stream without clients knowing any better. In North America, ESG regulation negates the possibility of dealing with ‘tainted’ materials.
- Lower geopolitical and trade risk: By integrating battery supply chains within NAFTA or the EU, geopolitical and tariff risks are reduced. When relying on China, the West risks a changing geopolitical climate and uncertain import and export tariffs.
China is at least decade ahead of the rest of the world when it comes to lithium-ion battery supply. OEMs are currently establishing their supply chains and look to China as the ‘cheapest’ alternative, but have they quantified the value of these other benefits?
Most may be chasing short-term solutions, kicking the can down the road, on the battery supply chain. By spending more money on developing an integrated supply chain in the West, we will reap the long-term rewards of an environmentally friendly, secure, local battery supply chain which will bring employment, technology and economic benefits.
If we do not, the future belongs to China.
Trent Mell is the CEO of Electra Battery Materials Corporation.