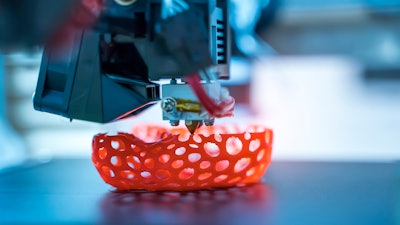
Thomas Jefferson once said, “I like the dreams of the future better than the history of the past.” Given what we have all experienced over the past 2+ years, I tend to agree with Mr. Jefferson. Looking ahead in 2022, here are five trends I predict for the world of automation and control.
Reshoring
Over the past two years, we have seen everything from runs on toilet paper to an extensive semiconductor chip shortage. The chip shortage has led to a massive bottleneck in manufacturing. From cars to consumer electronics, all manufacturers are feeling the pressure.
The majority of the world’s semiconductors are currently manufactured in China and Taiwan. Increases in demand, supply chain issues, and raw material shortages have all contributed to an increase in the number of manufacturers looking to reshore their factories in North America. A recent trade deal between the United States, Mexico, and Canada has further enticed manufacturers to bring factories back to North America.
Reshoring will increase the demand for automation, as manufacturers will need to incorporate additional automated processes to remain competitive against low-cost labor markets and compensate for employee shortages. According to a recent Reuters article, robot sales in 2021 hit a record as more manufacturers examined the potential to ramp up production using robotics. From January through November, 29,000 robots were ordered at a value of $1.48B, a 37 percent increase over the same period in 2020.
Increased Focus on Cybersecurity
News reports of ransomware strikes against American utilities have highlighted a need for increased cybersecurity. Last year, Colonial Pipeline was infiltrated by a group of Russian hackers via the VPN network that employees used to remotely access their system. The ransom was paid with bitcoin, and since then hackers have become even bolder, continuing to attack infrastructure, manufacturers, and private citizens. It is increasingly imperative that companies implement a very strong and agile cybersecurity plan to protect their assets and operations.
Traditional vs. Additive Manufacturing
3D printing has taken the world by storm in recent years. With advancements in tooling and filaments, the technology has come a long way since the concept of 3D printing first originated in the 1940’s. Today, we see 3D printing being used as additive manufacturing, creating industrial prototypes faster and with higher accuracy.
As the list of printable materials continues to grow across all mediums, companies need to ask themselves what mix of traditional manufacturing vs. additive manufacturing makes sense, and how fast should they integrate the new technology. Some hearing aid manufacturers in the United States have transitioned from traditional to additive manufacturing in less than two years, increasing manufacturing flexibility and allowing greater customization.
The Importance of Predictive Maintenance
Predictive maintenance has been around for a very long time, but in recent years there has been an enormous increase in the need to collect data from every aspect of the industrial manufacturing process. Every step in a manufactured product’s journey is analyzed. Sensors monitor vibrations, temperatures, noise, humidity, and so on, to decrease waste and loss by ensuring that a line is working at peak efficiency. Condition monitoring systems report when a bearing or a motor is reaching the end of its life cycle.
Gone are the days of sending a technician onto the floor to perform routine scheduled maintenance on a motor just because the calendar says to do so. With the ability to monitor every aspect of that same motor’s performance, we now know exactly when it will fail and when we should order ahead to replace it. This means fewer line down situations or reductions in line production, minimizing loss to plant throughput.
Sustainable and Environmentally Responsible Practices
Manufacturers are far more environmentally conscious than they were just 10 years ago. Much of this has been driven by consumer buying habits. Consumers today are far more likely to purchase products that are made of sustainable materials from reputable manufacturers who take their environmental responsibilities seriously.
To further this trend, the higher costs of energy and resources are driving manufacturers to adopt more environmentally sound processes. By adopting a total lifecycle view of the entire manufacturing process, the product itself, and the resources and raw materials, manufacturers help minimize negative effects on the environment.
As we embark on another trip around the sun, the new year is full of promise. The future of automation and control is brimming with new opportunities to develop superior processes and deliver better products to customers. With a lot of effort and a little luck, these trends of 2022 could allow “the dreams of the future” to become reality, improving the way we work and live for years to come.
Eric J. Halvorson is Partnership Marketing Manager II – Strategic Programs at Digi-Key Electronics. Digi-Key is a leading distributor of electronic components and automation products