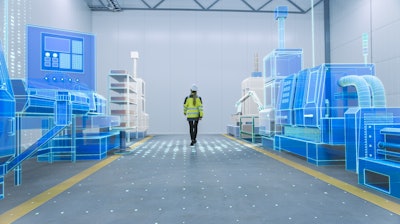
Factory floors are inherently complex environments, characterized by heavy machinery and demanding physical workloads. Workers in these settings must have the necessary skills to navigate their daily tasks safely and efficiently, minimizing the risk of injury. Even a minor lapse in safety can have significant consequences for both the injured employee and the business. For example, over 800,000 non-fatal and 18,000 serious injuries occur annually in the manufacturing sector alone.
Moving beyond traditional, passive learning methods like classroom instruction and reading, organizations in the manufacturing industry are embracing a modern approach to training their field workers: the adoption of virtual reality (VR) technology.By integrating VR, manufacturers can enhance safety in their environments, fuel innovation, improve knowledge retention, and reduce training and operational costs.
From Sci-Fi to Real-World Simulations
For an industry established and reliant on legacy technologies, the integration of VR technology is a relatively new concept. Cost and complexity are frequent apprehensions, as business leaders are hesitant to adopt technologies that require higher costs of change and longer downtime. However, modern VR software looks to effectively mitigate both.
Leveraging VR, training can be more effective. For example, trainees operating on factory floors will not need to wait for an assembly line to stop in order to receive training. Instead, both the factory floor and worker training can happen separately and simultaneously - contributing to the business scale without adding additional costs.
The propagation of advanced hardware, coupled with the intuitive nature of immersive software, further reduces the complexity of VR as a training solution. With modern VR technologies, organizations can eliminate passive learning techniques by replacing manuals and re-engaging workers. In a highly competitive environment, manufacturing leaders need strategies to enhance precision, speed, and flawless execution for their teams. VR is not just a futuristic gaming device; it is a powerful tool that transforms how skilled professionals train, work, and ultimately drive bottom-line success.
Fueling Efficiency on the Factory Floor
- Remote Collaboration. Experts can guide trainees globally in real-time. Train workforces of any size across locations simultaneously, ensuring consistent skill development and adherence to best practices, regardless of distance.
- Zero-Risk Refinement. Trainees can practice complex procedures and equipment interactions in a safe, virtual environment, eliminating real-world risks like improper assembly or injuries. Workers can also practice in hazardous scenarios or infrequent events that would be impractical or costly to replicate in the real world.
- Immersive and Engaging Training. Trainees and instructors have opportunities to operate in virtual factories to test and optimize workflows, providing engaging hands-on experiences that mirror real-world scenarios. Trainees can effectively boost skills, knowledge retention, and confidence in a fun and safe environment that encourages innovative thinking and problem-solving.
- Data-Driven Optimization. Virtual environments enable workers to simulate machinery wear and tear to anticipate failures, enabling data-driven optimization. Instructors have unique opportunities to track individual performance data within the virtual environment, identify areas for improvement, and tailor training programs accordingly, potentially preventing costly accidents before they occur.
Beyond mere visuals, VR's true power lies in shaping the future of how we build and sustain. From crafting intricate micro-components to navigating complex systems, VR delivers a hyper-realistic training experience that equips the manufacturing workforce to tackle new challenges. Workers immersed in these virtual environments retain information better, contributing to an overall 83 percent reduction in production costs.
VR technology empowers manufacturing and maintenance with key capabilities, including:
Manufacturers are actively seeking innovative strategies to remain at the forefront of the industry. VR offers a strategic advantage in achieving end results by enhancing worker safety, fostering innovation, and significantly reducing operational and training costs. Organizations can unlock their full potential, propelling them towards industry-leading safety, efficiency and innovation.