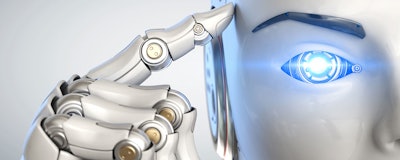
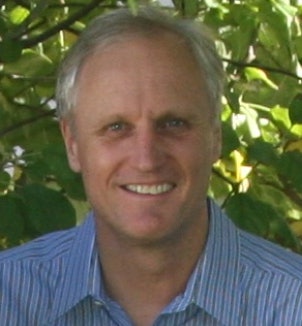
Back when I worked as a machinist running Davenport screw machines, it was up to us—the machinists, the line managers, and the supervisors—to monitor the processes and equipment to keep the line up and running. Together, we knew what to watch for and how to monitor the machines (and the people) to make sure they were operating at peak efficiency. We knew how to tell when a piece of equipment—a drill bit for example—was nearing its replacement phase or if there were any residual effects from variations in material chemistry. The cost of a single broken drill bit could be significant, as the subsequent tap and chamfer tools would also break, production parts would have to be scrapped or reworked, and the machine would be down as we replaced all of the broken tools.
For this, and a multitude of other situations, we collected what data we could, tracking everything from minute variances in finished parts to the training levels of our operators. As much as possible, we used that information along with years of accumulated experience to make the best decisions for the business: Was it time to switch out the drill bit? Did the change in materials affect something we hadn’t foreseen? Should we shut down the production line?
The adaptive intelligence (AI) that we’re getting to know today, would have eased our minds and given us the ability to make better and more consistent decisions. But back then, AI wasn’t a choice for shops like ours. To have AI in our business meant we’d have to fund the work of several highly paid computer engineers and data scientists who would then hand things off to a battalion of IT professionals tasked with managing and maintaining the software and systems.
And then there was the hardware. The cost of purchasing and maintaining machines that could support AI were tremendous—even the sensors used to monitor the manufacturing environment were costly.
All in all, AI has been the province of manufacturing giants with huge volumes and hefty R&D budgets—a luxury that other manufacturing businesses simply could not afford.
Until now.
Today, AI is more accessible to a wide range of manufacturers due to three core reasons: lower costs, easier access to data, and cloud computing. Here’s why:
Lower Costs Open Opportunities
Good news for manufacturing shops of all sizes—the cost of computer technologies continues to drop, breaking down the first barrier to AI entry. Everything from memory chips, computing power and storage are cheaper and better today thanks to miniaturization and mass production. The trend continues, now including hardware sensors to monitor your environment, and enable the Internet of Things (IoT).
As for those specialized data scientists and software developers? They’re still at work, but their contributions have hit the mainstream. AI applications are now packaged such that the requirements for deep programming are minimized for everything other than the most complex scenarios. Connecting has never been easier, and the systems work together to optionally automate execution as confidence in the recommendations increase.
All this is great, but it doesn’t matter how many sensors and applications you can afford unless they are positively impacting business outcomes.
Access to Multiple Sources of Data, Made Easy
Decisions are only as good as the data they’re based on, and for AI to positively impact business outcomes, the intelligence must be based on the right data. Fortunately, getting the right data today is much easier. Most production equipment now comes sensor-enabled, and connecting the devices can quickly bring streams of the necessary data.
That said, the traditional view of not looking across business silos will continue to limit the benefits. Manufacturers must expand their thinking to look at non-traditional sources of data, including ERP for contextualization, along with customer, operator, supplier, and product data for perspective. Looking across business silos for related data will help enable the system to better predict results.
If only you could do this quickly and without costly trials.
Send in the Clouds
Now you can. Perhaps the most intriguing technology advance in recent years is the fast-growing presence of cloud computing and software as a service (SaaS). One of the beauties of cloud is that you can try out an application, and quickly confirm if a new idea will work for your business. I particularly like what I call the “what can it hurt?” factor. Instead of spending months or even years setting up an implementation only to find that it just doesn’t work for your business, you can initiate a cloud application today and have it up and running through its paces in weeks or even days. You get to test-drive the application with your data, in your working environment.
For this, I recommend a relatively straight-forward task, such as replacing our worn-out drill bit. You could automatically monitor the equipment for slight changes in sounds or the product dimensions to predict when the bit should be changed. The benefit of using AI to actually drive improvement has begun. From there, it’s a short walk to auto-ordering the bit and scheduling the best time to replace it—preferably while the operator is away.
Now that you have the new drill bit in place and the right data in front of you, it’s about how you act on the data. Here’s where you pull in AI: Connect your data with the technology, and the data can be analyzed to create “if-then” models for action. You can be proactive rather than reactive in your business decisions.
Bottom line: higher yield, lower costs, better results.
How to Get Started?
Try it. Take it for that “what can it hurt?” test drive. First, find a vendor to set you up with industry use cases specifically demonstrating how manufacturers use and benefit from AI. Then hop a cloud and try it out with your data, with your processes, in your environment, for your business.
Before? It made good business sense to leave AI to the huge conglomerates. But today, AI is moving toward the masses.
Take a look. Things are different now.
John Barcus is vice president of manufacturing industries within Oracle’s Industry Solutions Group.