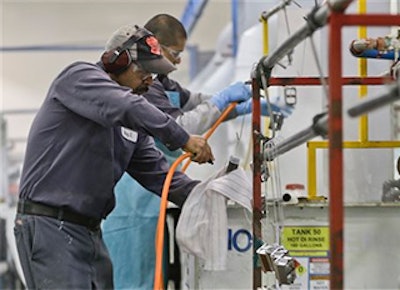
Communication.
It is the single most effective tool in any facet of business, especially in the area of workplace safety.
Today, with a workforce that is more distributed and more mobile than ever before, safety managers are facing huge communication barriers; static boards that read “X number of days since an accident,” email blasts that many employees rarely see and posters nestled in the corners displaying rules and safety regulations for that particular area just don’t cut it anymore.
ALSO READ: Connect More Employees and Provide More Data
In order to overcome these barriers, companies need to embrace the digital era when it comes to the communication of safety hazards, guidelines, rules, regulations, warnings, goals, and progress reports by broadcasting them in an up-to-date and in real-time manner across an array of mediums in, and out of, the workplace.
Safety communication is an extremely important, and often overlooked, facet in businesses; but a safer workplace leads to a better bottom line.
Workplace Safety in Action
Alcoa, the aluminum manufacturing giant, is the best of example when it comes to demonstrating the correlation between workplace safety and the bottom line.
The year is 1987, and newly named CEO, Paul O’Neill, begins his first speech with “I want to talk to you about worker safety.”
The statement quickly hushed a room expecting to hear about revenue projections and O’Neill’s plans for increasing profit margins. It was as if O’Neill knew something they didn’t; in his mind, focusing on that one key habit, safety, would change the entire company culture and have a positive effect on the bottom line.
And change it did.
One year after naming Paul O’Neill their CEO, Alcoa boasted record high profits. Over O’Neill’s 13 year tenure, lost work days to injury per 100 workers went from 1.82 to 0.2 — a staggering decrease of 89 percent — and Alcoa’s annual net income was five times higher than when he began.
Enacting an effective safety program that fosters an open safety culture that reaches workers inside, and outside, the workplace and includes up-to-the-minute safety notifications, hazard communication, and productivity updates can drastically increase worker productivity, lead to fewer safety claims, lower workers’ comp costs, and an improvement in employee morale.
Workplace Safety Musts
In order to see the improvement in company culture, companies need to take the time and necessary steps to ingrain safety mentality in their workforce. Constant reminders and safety warnings must be implemented to help this transition take place.
The safety mentality begins with the leaders. Employees must be able to trust that their supervisors have safety as the number one priority and that they are able to report to them if they notice any unsafe activities or behavior. This communication channel is key, especially for those that have employees spread across a vast area.
This culture does not happen overnight, a successful transition to a safety centric workplace takes time. Companies can help smoothly enforce this transition move by consistently displaying safety reminders to supervisors and employees in unique, visually stimulating ways, across an array of digital screens.
The growing presence of Millennials in the workforce are conditioned to get their news and updates digitally, and companies are embracing this trend by utilizing digital signage messaging on large screens, desktop dashboards and mobile devices.
Workplace Safety History
Since President Nixon enacted the Occupational Safety and Health Act, or OSHA, on December 29, 1970, occupational deaths and injuries have been cut by 62 and 45 percent, respectively.
The top 10 areas for which they issue citations are: forklifts, hazard communication, electrical wiring methods, electrical system design, guarding openings, exits, mechanical power transmission, respiratory protection, lockout/tagout and portable fire extinguishers. These problems stem from lack of training to poor signage, improper implementation to inadequate equipment, and no action plan to low visibility.
Companies have come a long way in means of safety communication since OSHA was first enacted, but there is still a lot of room for improvement to achieve the goal of completely eradicating occupational deaths. By embracing the digital age and utilizing the technology to broadcast live updates in means of hazard communication and mechanical training, companies can take the step forward to reaching that goal
Workplace Safety Future
At RMG Networks, we are ushering the new wave of digital connectivity and bringing it the workplace, and allowing everyone to be connected anytime, all-the-time. We hope to help pave the way towards fewer accidents in the workplace, and help companies take that giant leap towards a safety centric culture.
Our system collects, analyzes, and prepares data that presents in real time via desktops or mobile devices to managers for them to take immediate action. We also utilize large screen displays strategically placed throughout company offices and warehouses that allows workers to see real-time metric information as well as safety tutorials and regulations for a particular area that are highly visible, color-coded and easy-to-read — transcending language barriers and allowing workers to truly motivate and educate themselves.
Connectivity is essential when it comes to the future of workplace safety, which is why we designed a digital signage system that is easy to update and can be used to reach all employees whether they are within the confines of the factory, or out in the field; transcending a multitude of barriers.
Workplace Safety Takeaway
Fostering a truly safe environment begins from within. In order for the transition to be successful, all communication channels must be up-to-date, highly visible, and visually stimulating.
By utilizing the newest technological advancements and implementing them in the workplace, safety messages can reach 100 percent of all employees quickly, and effectively. Today, more and more companies are implementing safety as one of its core values, and they are seeing a great improvement on their bottom line. In fact, according to an OSHA study, for every dollar invested in safety communications, a company saves $4-6.
The days of the static messages that often go overlooked are over. In order to break through the noise, safety messages must be visually stimulating and up-to-the-minute that provides employees with instant reminders and notifications.
Steve Chang is Senior Vice-President of Strategy and Solutions at RMG Networks.