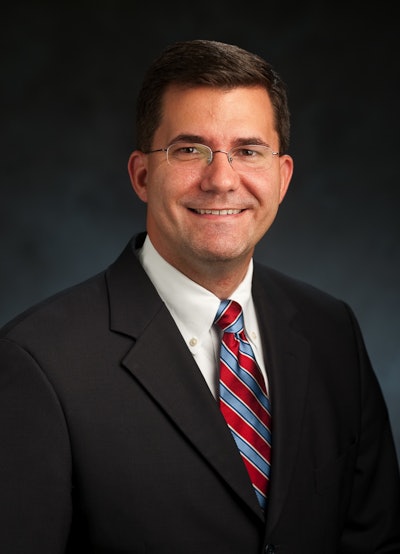
In-house legal teams are faced with product recalls from time to time, especially in the consumer products sector. If you’ve been through a recall, you know it’s something to avoid if at all possible. Creating a culture of product safety within an organization is a strong line of defense against recalls. But how is this accomplished? Below are five tips to help you shift your organization from complacent to compliant.
1. It’s All About The data
Data is more available than ever before and your company’s ability to obtain information quickly about a potential product issue helps to isolate the problem, be compliant, and take action. Make sure that you have a streamlined way to collect and report on consumer complaints, production problems, product testing reports, warranty returns, insurance claims and product liability lawsuits, as well as reports from watch dog sites. Monitoring product safety requirements is also a valuable way to avoid recalls. It’s important that in-house counsel regularly check liability statutes and cases to ensure the company’s products are suitable for use and in compliance with federal, state, and international requirements.
2. Manage The Supply Chain
In today’s global economy, raw materials come from diverse providers all over the world. In this environment, it’s critical to have systems in place that can ensure that the specifications of raw materials and component parts meet all relevant statutory and regulatory requirements. One way to do this is with
a supply chain management database that provides solid visibility and record keeping at every touchpoint, including testing. In addition, following due diligence requirements for component part suppliers can prevent problems with the finished product. Best practices include reviewing the component part certificate, asking questions about testing and certification, requesting written test procedures, spot checking a supplier's test results, and site checks to a supplier's factory or third party laboratory.
3. Consider An Internal Compliance Program
There are some obvious signs that an internal compliance program is needed. If you’ve had multiple previous recalls and/or requirement violations over a short period of time or failure to timely report product hazards, then a program might be beneficial. Another indicator of the need for a compliance program is if there is evidence of insufficient controls for preventing manufacturing and distribution of dangerously defective or violative products. When creating a compliance program it’s important to have written standards and policies as well as a mechanism for employees to confidentially report compliance related questions and concerns. Next, make the written guidelines available to employees and bring the program to life with training so that staff understand the program’s intricacies and requirements. It’s recommended to keep compliance records for five years and, if applicable, to involve the board in compliance oversight.
4. Get Senior Management Buy In
Creating a culture of product safety starts at the top. By keeping senior management apprised of product issues and failures and providing timely reports on compliance challenges, you can ensure that executives become engaged in the oversight. Also, asking them to monitor, document, and review internal compliance programs periodically will strengthen the program and encourage employee adherence.
5. Make Reporting Bullet Proof
When a regulatory body is asking for data that cannot be provided easily, it can turn an organization upside down. Having a system of internal controls to ensure a company promptly, completely, and accurately reports required information to the agency upon learning of a substantial product hazard can increase compliance.
Promoting a culture of product safety inside and outside the company means devoting resources to develop, maintain, monitor and improve the company's compliance program. Having this infrastructure can help defend against recalls. However, there are instances in which even the most buttoned up and safety focused organizations face a recall. In this situation, legal teams need to work closely with senior management and recall experts who can help to streamline communications with consumers and agencies for a faster resolution to the event.
About the Author Mike Rozembajgier is vice president at Stericycle, where he has held multiple management positions. Prior to joining Stericycle, Mike held various management positions at Guidant Corp. (now Boston Scientific) and at Deloitte in their Strategic Consulting practice.