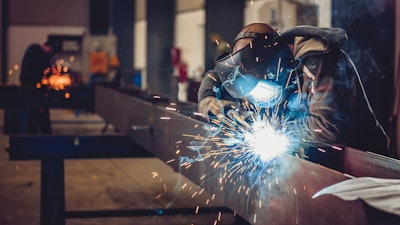
Metalworking is a high-precision process. Machining and welding require fine movements despite encountering a considerable amount of friction, and even small mistakes can create significant workflow disruptions. Many facilities have turned to metalworking automation as a solution.
While humans have worked metal by hand for centuries, if not millennia, automation is the new standard. It’s easy to see why, too, when considering automation’s advantages in several key areas.
Error Reduction
The biggest precision benefit of metalworking automation is its tendency to prevent errors. More than 80% of failures and defects stem from human error. Metalworking is highly prone to these mistakes, too, as it’s a highly repetitive, physical process.
Automated systems cannot get tired, bored or distracted. They also cannot make momentary lapses in judgment because they operate off of the same data every time they perform an action. Robots aren’t entirely immune to mistakes — sensor defects and non-standardized processes can hinder their accuracy — but they dramatically reduce errors compared to humans, improving overall precision.
Finer Motor Control
Automated metalworking machines are also inherently more precise in their movement than humans. Smaller tools allow CNC mills and other systems to make movements smaller than physically possible with human hands. Some equipment can even work in sub-micron dimensions, making changes too small to see with the naked eye.
This fine motor control and minuscule movement do more than enable the production of smaller metal products. It also means any process deviations create less of a noticeable impact and that more intricate designs are possible.
Consistency
Automated metalworking systems also improve precision by being more consistent. An experienced metalworker could match a robot’s accuracy and speed in some cases over a short period. However, they’d eventually become tired, leading to slow-downs or mistakes. Robots don’t have that risk.
As long as the sensors within an automated system are working, the machine will deliver the same level of quality every time. This consistency means even machines that may be less efficient or precise on a small scale will produce better results over time. Combining that reliability with automation’s error reduction and fine motor control leads to considerable improvements.
Skill Shortages
Automation can stir up uncomfortable feelings in blue-collar industries like metalworking out of job loss fears. However, manufacturing faces a shortage of millions of workers, so robots aren’t taking jobs as much as they are filling those humans aren’t. This ability to address skills shortages has precision and efficiency benefits, too.
Metalworking shops can still accomplish a high volume of quality work despite labor shortages through automation. Freeing humans up from repetitive work also lets employees focus on tasks they find more engaging, leading to improved precision in those areas. Consequently, even the roles automation doesn’t perform can improve as a side effect.
Steps to Capitalize on Metalworking Automation
Recognizing the benefits of metalworking automation is just the first step. You’ll need to approach this technology carefully to experience these advantages for yourself. That requires attention to a few best practices.
Start Small
One of the biggest obstacles to automation is its cost. While robots have become more affordable over time, 71% of manufacturers today still cite upfront expenses as their primary barrier to automation adoption. The improved precision and efficiency will compensate for those costs over time, but the key to capitalizing on that ROI is starting small.
Avoid the temptation to automate an entire workflow at once. Start with a single process. This target should be wherever you can benefit most from automation’s unique advantages over manual alternatives. These tend to be highly repetitive, detail-oriented or error-prone tasks. Automating these will produce a more significant ROI, enabling further tech adoption.
View Automation and Humans as Complementary
Next, it’s important not to overestimate metalworking automation’s potential. As impressive as this technology is, human employees are still better in some respects — namely, they’re more flexible and better at outside-the-box thinking. You’ll get more out of robots if you view them as a complement to your workers instead of a pure replacement.
Automate repetitive and highly physical tasks. Then, assign your now-free employees to less predictable roles. Sometimes, these workflows are related. For example, you may need to use employees to ensure materials are good enough and components are in the right place for robots to machine them accurately.
Prioritize Maintenance
Getting the most out of your automated metalworking equipment is also a matter of maintenance. Falling into disrepair or out of calibration is one of the few scenarios that can cause automation to become imprecise and unreliable. You can preserve their benefits by paying close attention to their maintenance needs.
Using Internet of Things (IoT) sensors to enable condition-based repair is one of the most important steps. However, maintenance also relies on proper setup, not just breakdown prevention. For example, suboptimal bandsaw blade tension will increase blade wear, hindering precision and causing issues down the line. Avoid that by following OEM specifications for your equipment and specific materials.
Use Data to Your Advantage
Robotic systems are also at their best when you use them in conjunction with other technologies. More specifically, automation should be part of a larger, data-driven digital transformation. The more workflow data you collect, the more reliable you can make these machines.
Gathering data from automated quality inspection is one of the most impactful examples. Trends in this information can reveal where defects stem from, informing workflow changes for higher precision. Analyzing data from your robotic workflows will also help you see which automation steps produce the best results and where you need improvement in future automation projects.
Don’t Overlook Training
As you automate metalworking processes, be careful not to ignore the human factor, too. Automation inevitably means your employees’ day-to-day work will change in some way. Failing to prepare them for that shift could disrupt workflows and delay a positive ROI.
More than a third of organizations cite limited knowledge or skills as a barrier to AI and automation. You’ll need to train your workers to use, maintain and work around automated machines if you want to use robots to their full potential.
Metalworking Automation Is the Future
Metalworking automation is becoming the new norm, and that shift is a positive one. However, you won’t experience automation’s benefits automatically. At the end of the day, it’s like any other tool in that it requires proper usage to produce results.
When you know what these machines offer and how to implement them effectively, you can automate your workflow to its fullest extent. That will help you become as precise and efficient as possible in an increasingly competitive environment.