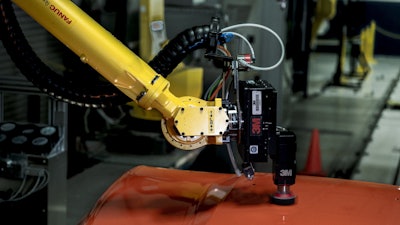
3M has a relatively small consumer business but at its core, it’s a big industrial, B2B company.
That’s according to Carl Doeksen, global robotics and automation leader at 3M, one of the largest manufacturing conglomerates in the U.S. He describes his company’s approach to industrial automation as two-pronged.
“First of all, it’s certainly for our own supply chains and our own factories. We have hundreds of factories around the world and that’s important to 3M for safety, quality and productivity,” said Doeksen. “But we’ve seen in recent years that our industrial customers are demanding automated and robotic solutions for these traditional applications that 3M is the leader in, like grinding, polishing, deburring, sanding, dispensing structural adhesives, applying industrial tapes, packaging solutions and, in some cases, industrial films.”
Industrial Equipment News recently spoke with Doeksen about 3M’s work with BMW, some of the trends he’s seeing, and how industrial automation is helping manufacturers address demographic shifts and labor shortages while opening up new opportunities for their workforces.
The following transcript has been edited for length and clarity.
IEN: 3M’s products are playing a role in BMW’s production processes for inspecting, rework processing, and marking painted vehicle surfaces. Can you provide some more detail?
Doeksen: In automotive assembly, [BMW] tends to lead automation. In those factories, they’ve successfully automated welding, painting and undercoating with robots. But all of their sanding, polishing and deburring is still done with human operators at nearly every assembly plant in the world.
[BMW] told us, “We love your sandpaper, we love your polish, we even love your portable power tools. But we’ve got really high turnover in that department.” When you see that operation, it’s called the finesse deck. It’s named after the 3M Finesse-It system, which is the leading manual system. But now they’re the first ones to have done it with robots.
And that was not easy. But working together, we figured it out. And I would say that, during the pandemic, that project accelerated because when they’re doing that final inspection of the clear coat, the car is literally swarmed with dozens of human operators working in very close quarters. [BMW] wanted to automate this and now they’ve done it.
IEN: Are high turnover rates a topic of discussion for a lot of manufacturers when talking about automation?
Doeksen: Yeah, and one of the things I always harp on it, in the automation industry, there tends to be an overemphasis on cost and pulling labor out of the process. But let’s talk first of all about creating a safe work environment, and then the quality, predictability, the data and the analytics that they have access to when compared to human operators doing the work.
From a management and engineering perspective, a robot creates a much more data-rich, predictable and quality-controlled environment than a human operator. Especially when you have high turnover in the department; that’s a killer for quality and productivity.
IEN: When these processes are being automated due to high turnover or labor shortages, does it create new roles for people in the manufacturing space?
Doeksen: Absolutely. If you’re working in automation, if you’re a technician who is troubleshooting the robots or keeping the robots running, you tend to be in a higher job band than you were as an operator.
Athena Manufacturing in Austin, Texas was doing all the grinding but now they run those robots. [One of the operators] had his picture in the Wall Street Journal and he shared it with his family. It’s a great story about how that robot has really transformed his life. The blue-collar shop floor is full of stories like that.
[Athena] is putting out more parts than they used to. The parts are better quality and the bosses have better data on what’s going on in the department, and he’s a happier guy. And I can tell you that the safety manager in the plant would rather have him running…the robot than grinding all day with that heavy Milwaukee equipment.
3M Finesse-It robotic paint repair system3M
IEN: How has the conversation around automation changed in the past five years and how do you see it changing in the next five years?
Doeksen: When I first got involved with the robotics industries, we spent a lot of time in meetings with committees and associations talking about how robots aren’t taking over the world and they’re not stealing jobs. The mainstream media really liked that story. “Amazon is introducing Amazon Go and it’s going to obliterate every retail job on the planet.” But I really felt the pandemic changed that narrative. All of the sudden, even in the mainstream media, the robots are your friends.
In the next five years, what I and my peers see happening is a penetration into the small and medium shops. That’s one of the beauties of 3M. Our industrial model, the heart and soul of it, is the small- and medium-sized shop. In the past 40 years, the big companies, especially in electronics and automotive, have adopted industrial robots.
We have an investment in GrayMatter Robotics in Los Angeles. They’re just one example of a company that’s focused on smaller and medium sized companies. So, the robots have to be easier to use and you need the right integrator. And there are some of those popping up that are focusing on this market. So, I see explosive growth as the automation industry for the first time genuinely takes the small and medium shop seriously.