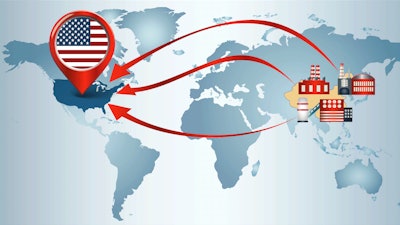
The COVID pandemic has led the U.S. industrial sector to take a hard look at the efficiencies and cost-effectiveness of operations and supply chains. While production improvements can be addressed by implementing process improvements, updating infrastructure, upgrading IT platforms, and making equipment investments, supply chains are obviously more complicated.
Enhancements in this arena need to offer efficiencies that are realized not only on a day-to-day basis, but in realizing business continuity goals related to unplanned events, like a pandemic. With this in mind, we offer the following collection of articles and interviews that look at reshoring as a potential solution. In addition to examining a potential reshoring surge, we’ll also investigate the challenges that remain in bringing more jobs back to the U.S.
Ethan Karp is the President and CEO of MAGNET - the Manufacturing Advocacy and Growth Network. The organization is dedicated to helping manufacturing businesses compete globally by expanding local operations. He believes that recent events will trigger a tremendous amount of conversation about reshoring, and recently sat down to discuss the competing mindsets that place a return of U.S. manufacturing’s heyday against the consumer-driven demands of lower-priced goods.
Jeff Reinke, editorial director: What do you feel are some of the driving forces behind re-shoring conversations?
Dr. Ethan Karp, President and CEO – MAGNET: Let’s start with the obvious benefits. Buying local provides supply chain security, protection from disruption, reduced lead times and potentially higher quality. But buying local has other benefits that are less obvious, starting with protection from IP issues, as rampant Chinese IP infringement and stealing ensures products made overseas will be knocked off quickly.
Another less-obvious benefit is that suppliers and buyers being geographically close can lead to rapid innovation and iteration on product design and production-process optimization. Finally, buyers can help their own communities because the local products they’re buying can lead to jobs. This is especially relevant where an industry serves a local community.
JR: Is there a way for states or regions to try to compete, or are companies pre-determining the sites of the re-shored jobs?
EK: States can compete by providing incentives that lower the risk of a company investing in the automation and equipment required for re-shoring. Whether this is through loan-loss guarantees, grants, below-market financing or even tax incentives, companies are more likely to enter markets previously only served through overseas competitors when upfront investments are easier.
JR: Which industries are seeing the biggest uptick in re-shored jobs?
EK: Except for companies who make PPE, no industry is seeing a major uptick. Most companies are considering re-shoring, but many do not know how to approach it -- especially given high switching costs associated with changing supply chains.
However, the potential for future products and new versions of products to be engineered in collaboration with domestic companies is the most likely path for re-shoring, albeit over a longer period of time. Typically, companies who collaborate in designing a product will eventually produce those products, and no switching cost would be incurred in this scenario.
JR: Are there specific supply chains that are triggering decisions to re-shore?
EK: It’s not really about specific supply chains, although there are many supply chains that will be very hard to re-shore, at least initially. Electronics is a great example. Not only are many electronics assemblers overseas, but sometimes the entire supply chain is co-located around assemblers. Re-shoring would require bringing not just one type of company but an entire industry.
JR: COVID is definitely having an impact on reshoring trends – do you think these moves will be short or long-term?
EK: This is the billion-dollar question. There have been movements in the past to "Make it in America" that didn’t have the staying-power that manufacturers would have hoped for. What makes today different is that the supply chain disruption experienced by many through the COVID pandemic was much larger than anything manufacturers had experienced.
Secondly, the urgency fueled by inadequate supplies of PPE and our inability to rapidly produce them en masse increased awareness that manufacturing in America is important.
Finally, ongoing trade concerns with China, rising labor costs, and uncertainty in future public policies that may penalize overseas production could just be enough to make companies seriously consider more stable local supply chains. We are certainly closer than ever to long-term re-shoring, but only time will truly tell if U.S. manufacturing will take back what it has given away over the last 30 years.