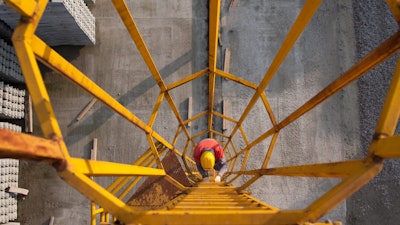
Ladder Safety remains a top concern for facility operations and their maintenance crews. The Occupational Safety & Health Administration (OSHA) believes that injuries caused by improper use of ladders are 100 percent preventable. As recently as 2017, an update to the 1910.28 Walking Working Surface standard has the potential to affect facilities across all industries.
Before discussing regulatory compliance updates and timelines, it is important to understand why ladder safety has remained a top concern in recent years. OSHA releases annual reports, and ladder violations remain in the top 10 citations given by the authority every year. In the general population, it is estimated up to half a million people visit the emergency room annually for ladder-related injuries. Some sources claim that roughly 80 percent of falls among construction workers involve a ladder.
Unfortunately, approximately 300 people die every year of fatal injuries incurred from falling off a ladder, with most ladder deaths occurring with falls under 10 feet. If OSHA is correct with their statements that 100 percent of these deaths were preventable, then action should be taken in every facility to prevent any more avoidable injuries and fatalities.
As of November 2018, the update to OSHA 1910.28 mandates all newly installed permanent, fixed ladders in the United States over 24' in height be equipped with an OSHA-compliant ladder safety system. Cal/OSHA (for California only) has the same requirement, but for ladders over 20' in height. For ladders that were installed before November 2018, there is a deadline to retrofit these ladders with a compliant solution by November 2036.
What is a Compliant Ladder Safety System?
Safety and maintenance professionals are familiar with the cages that have been historically installed on permanent, fixed ladders in facilities. These cages had the potential to provide areas to help workers lean against to rest while ascending or descending a ladder, but they provided no active fall protection to the user. They could prevent the user from falling away from the ladder during their fall, but there were no controls present to prevent the fall from occurring, nor protect the worker from injury or, worse, fatality.
In some cases, ladder cages could cause further injury to a falling worker before they made contact with the ground below. It’s important to know that these legacy ladder cages are not banned now and don’t necessarily have to be removed. But they no longer suffice as a means of fall protection for ladder climbers. And if they become a blockade for installing an OSHA-compliant solution, their removal would not diminish worker safety.
A ladder safety system is typically made up of steel cable or a rail assembly that runs the entire height of the ladder. These systems utilize a shuttle device that connects the rail or cable to the user’s body harness and provides active fall protection for the user as they ascend or descend the ladder. The system must have a brake and shock-absorption system that will sense a fall occurring, decelerate the user and successfully arrest their fall. Be sure to consider the user’s existing harness and make sure it has the necessary components installed.
Most ladder safety systems require a chest or waist d-ring on the user’s fall protection harness to allow the user to properly connect into the system. It’s a common mistake that organizations will neglect verifying their existing fall protection harness’ compatibility with their newly-installed ladder safety system. Refer to the ladder safety system manufacturer’s specifications to confirm which harness D-ring location their shuttle device must attach.
As stated above, all permanent ladders 24' or higher built on or after November 2018 must have a compliant ladder safety system installed during the construction of the ladder. Eligible ladders that were built before November 2018 have until November 2036 to be retrofit with a system. However, if any part of a pre-2018 ladder must be repaired or replaced, the retrofit must occur at the same time. For the full OSHA code update, please visit www.osha.gov.
Benefits of Early Compliance
Ladders continue to be one of the (statistically) most dangerous parts of any given facility. But with a deadline as far out as 2036 to retrofit ladders, safety managers can have a difficult time convincing finance or management to approve the work so far out from the deadline. However, understanding the direct and indirect costs of a fall occurring might be the incentivizing detail missing from the conversation.
While it is impossible to determine the exact direct costs of a fatal or non-fatal injury, it is easy to assume that a fall injury will likely result in a visit from OSHA. If a visit produces an OSHA-deemed “serious” violation, they can cost over $16,000 in fines. That is not considering worker’s compensation payouts, increased insurance premiums, and potential litigation costs from the injury.
According to some sources, indirect costs related to an injury can be four times greater than the direct costs. Indirect costs can vary from decreased productivity among workers after an injury occurs, loss of business from damaged reputation, and time spent retraining other employees. Almost any ladder safety system on the market will be less expensive than the aforementioned violation cost, so a simple cost-benefit analysis might help struggling safety managers in their budget discussions.
Additionally, organizations should consider what is in the best interests of their employees to protect their safety and well-being. Remember that ladder injuries, fatalities, and violations remain at the top of OSHA’s annual reports because of their continued prevalence. The safety community can take an active role in preventing future injuries and fatalities by aiming to retrofit all eligible fixed ladders as soon as possible.
Philip Jacklin is Continuing Education Program Manager for Diversified Fall Protection. He is an AIA continuing ed provider, QSSP & OSHA-30 certified, and has been a partner to the fall protection industry since 2018. He can be reached at [email protected].