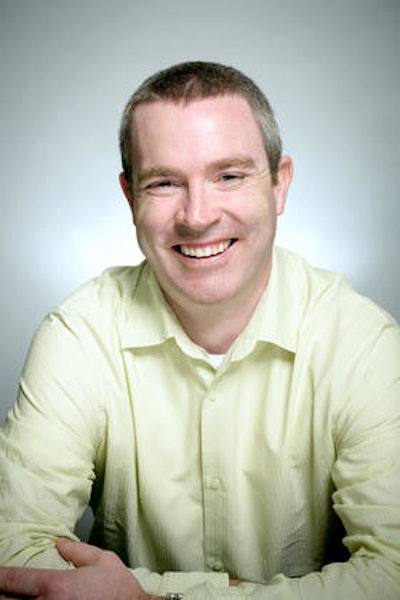
It’s a brutal, cost-driven world for manufacturers. Increasingly, those who don’t use Manufacturing Execution Systems (MES) to drive down variability and costs will be left by the wayside.
Given this, why don’t more people use MES? Sometimes it might boil down to confusion about what they are and what they offer.
MES gather granular information about current conditions on the plant floor that indicate to your employees how to make cost-saving process improvements. This happens pretty much in real time.
Your MES enables employees to run your plant more efficiently, the benefits of which are twofold. First, you can impress additional accountability, which increases employee engagement. Second, the increased efficiency decreases waste and variability and raises quality. At Factora, our costs to the client are often dwarfed by the savings we generate, as early as the first year.
Here are five more reasons to care about MES.
It's a great deal.
Admittedly, the thought of hiring consultants to improve shop floor processes leaves most manufacturers with fear of an endless drain of cash accompanied by strings of long words, earnest discussions and dusty reports.
No one has told you that MES can be implemented gradually, with each successful initiative helping to fund and build enthusiasm for the next. Not only that, the first initiative often bears the richest rewards. Why? Because a good MES consultant will aim for the project where the biggest return can be achieved for the smallest outlay— the resultant fruit can be very juicy.
It’s the only way to get out of your current tangle.
You can’t figure out how to get past the current operation you have, with several senior people involved in various aspects of running your shop floor, entangled with a number of Excel spreadsheets. With an MES, you’ll get visibility and insight. You get a clear, data-driven overview of where your costly problems are and how to address them. Think of it as an advanced, sophisticated way of making the solution obvious to all.
An ERP cannot do the job.
ERP is transaction-based and doesn’t work in real-time. ERP data, gathered crudely into time periods, lacks the granularity to help you identify and correct operational problems. Basically, ERP is financially driven; it focuses on gathering and summarizing financial data.
You don’t know what you don’t know.
Often, plant managers think that they are performing well because they are meeting current plant standards. The question is: are those standards reasonable? Current? Where did they come from? It’s guaranteed, the market will be driving costs down all the time, tightening your margins. You cannot control what you do not measure—without an MES, it’s almost impossible to know how well you’re really doing.
You're tired of throwing out cake.
For manufacturers, variability is the root of all evil. Decrease your variability and you’ll see your profits rise. As an example, a leading food manufacturer asked Factora to uncover the root cause of variability in cake height, which led to too much finished product being discarded. Our analysis uncovered variabilities in the baking process. Our MES solution is predicted to reduce batter consumption by at least 5% and also reduce finished-product waste. For the food manufacturer, it’s a perfect double play … now they can have their cake and eat it too.
Andrew Waycott is the Chief Operating Officer and Chief Technology Officer at Factora.