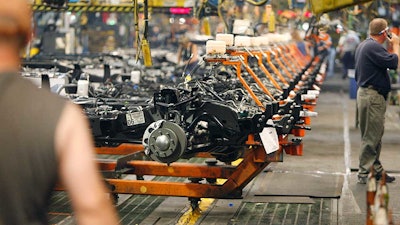
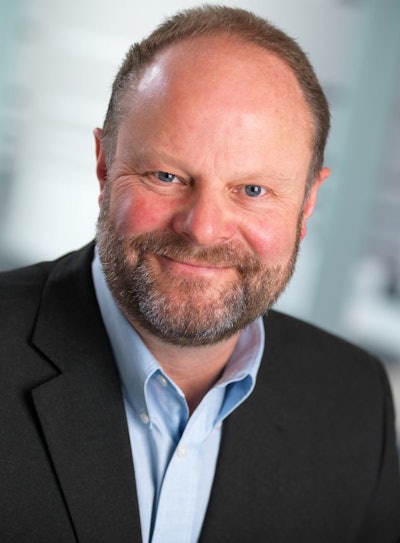
As technology advances, the performance gap between modern, state-of-the-art manufacturing facilities and older production plants becomes increasingly apparent. New installations may be bristling with sensors and continuous feedback loops that optimize the process on the fly (one component of so-called Industry 4.0 and the Industrial Internet of Things (IIoT)).
On the other hand, older manufacturing systems reflect technology and market conditions at the time when they were built, relying on experienced operators and maintenance teams, manual adjustments and post-production quality checks. Increasingly, we witness those older plants suffering from comparatively poor utilization, production throughput and yields; these factors and their impacts on operating costs reduce the ability of the manufacturer to compete effectively. Their markets are often facing increasing competition from elsewhere and the emergence of robotic manufacturing and further automation.
Often, manufacturers simply accept the limitations of their existing equipment; the classical alternative is to make a major capital investment in new manufacturing machinery. However, there are many cases where a smaller investment can offer the prospect of increased manufacturing performance through science-led engineering and some carefully selected novel process monitoring and optimization.
Some key examples of this include:
On-Line Product Monitoring
Many QC systems involve measurement of samples of finished product; whilst a batch test is performed, continuous manufacturing processes can produce large volumes, exposing the manufacturer to the risk that a significant volume of out-of-specification inventory is produced whilst the test is in progress. Using novel sensor combinations and technologies transferred from other industries it is often possible to perform a close equivalent to the final QC measurement, but with the advantage that it is on-line, real-time and at little or no risk to the production process.
This provides two key advantages. First, the moment the out-of-specification product is detected, the operator can take action to mitigate the problem or abort the process to eliminate further waste. Second, the continuous feedback can be used to provide real-time control of critical processes and improve production consistency and hence yield.
Applying The Latest Sensing Approaches To Key Process Parameters
Most processes have a handful of key parameters or machine settings that are critical to successful operation.
If these are not monitored sufficiently well (or are perhaps open to casual operator ‘fiddling’), then they cannot be considered to be well-controlled. The application of on-line monitoring can bring much-improved process understanding and control with a direct improvement in process performance.
Characterizing Manufacturing Processes
Older manufacturing equipment often relies on the gut feel of a highly experienced individual for its setup and maintenance.
This reliance on an individual presents a risk to the operation; techniques to apply rigorous engineering and analytics (capturing information on process temperatures, alignments, vibrations and acoustic signatures, motor currents and other critical parameters, correlating these with normal operation and various fault conditions) can quickly identify normal operating settings and conditions and then permit much more straightforward setup and fault diagnostics. This can even begin to extend to predictive maintenance.
In our work with major manufacturers in a number of industrial segments, we witness a spectrum of technologies from those that have changed little in decades, to those which represent significant investment in the latest equipment.
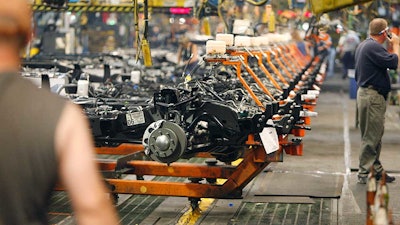
It is perhaps surprising that there remain many manufacturers who continue to operate as they have done for many years and who are unaware of the value (in straightforward return on investment) of a fresh engineering approach, based on current commercial off-the-shelf sensing and control technologies.
Before continuing to accept mediocre manufacturing performance or writing off an aging plant it is worth exploring the technology and measurements that are becoming available which, when applied appropriately, could have a dramatic effect on understanding and control of a production process.
In particular, it is worth considering the options to buy, build, adapt or innovate to improve existing machinery and how to identify the innovations that could deliver real economic benefits.
Andrew Strong is a UK Chartered Engineer and Fellow of the IET with over 25 years of research and industrial experience including in the high-tech manufacturing sector. More recently, with Cambridge Consultants, he has worked with clients to identify novel on-line measurement solutions for real-time process feedback, as well as novel manufacturing processes to replace legacy equipment.