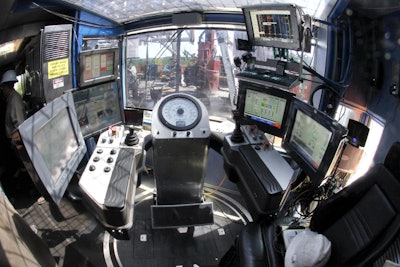
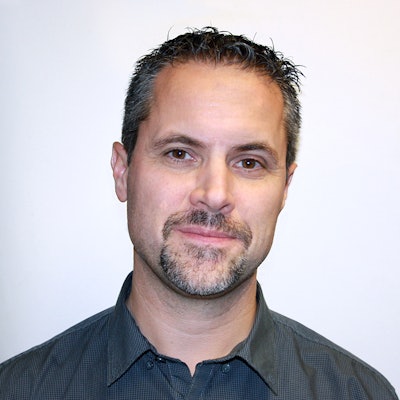
Smart factories are the manifestation of what's being called the Fourth Industrial Revolution — a concept that's been in the conceptual-buzz phase for years.
While the last revolution saw the widespread digitization of manufacturing technology, allowing information to be produced, replicated and shared on an unprecedented scale, the Fourth Industrial Revolution, or Industry 4.0, could take manufacturing to a place verging on self-awareness.
What does this look like? Smart components will interact directly with other devices — independent of human micromanagement and oversight. It means our technologies will be capable of building and interpreting a more nuanced understanding of the manufacturing environment. People and machines will have access to real-time virtual representations of all manufacturing functions.
It's a vision that's fast becoming a reality. Experts have expounded on the challenges, but this hasn't prevented early-adopters from making significant headways.
Growing Device Market
Smart manufacturing requires networks of connected devices, which are increasingly less likely to be your traditional smartphone or tablet. According to a 2015 article published by Stratfor, a geopolitical intelligence firm:
"There are now about two Internet-connected devices for each person on the planet, and that number could more than double within the next five years. Although most people tend to think of personal computers, tablets and smartphones as their main Internet-connected devices, these three categories together account for less than one-third of all connected devices. This share will drop in the future. To put the shift into perspective, just a decade ago personal computers accounted for more than two-thirds of all interconnected devices; now they account for less than 10 percent."
IOT Analytics estimates patent registration for Industry 4.0 products has increased by a factor of 12 in the past five years. Patents include cloud computing, augmented reality, 3D printing, Big Data systems, system security, humanoid robots and cyber-physical systems — all components for a more autonomous manufacturing environment.
Big Data Challenge
A major challenge for smart factory development has been an issue for technologies in all sectors: big data. Smart technologies need to store, process, analyze and transfer massive amounts of information. Volume isn't the only issue, though. Data types can also be a challenge. With so many different components from diverse industries and manufacturers being implemented in unique manufacturing environments, connecting them can be a challenge.
A WIRED article in 2015 reported that factories in Germany are already demonstrating how "plug and play" technologies can be applied to a "plug and produce" context for factories. These advancements will allow independent production modules to be rearranged in any order to suit final product outputs. According to Detlef Zühlke, director of innovative factory systems at the German Artificial Intelligence Research Centre (DFKID), "One day different modules in the factory could potentially drive themselves around to allow factories to alter the production line."
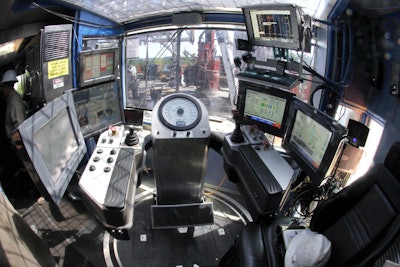
Automated Supply And Demand
Automation isn't just a goal for internal factory operations. Innovators are looking to integrate networks between factories as well. As a recent SAP video demonstrates, rather than having onsite technicians report problems and request parts or servicing from supplier representatives, smart components will have the ability to self-assess and report problems directly to manufacturers. Suppliers will be able to implement just-in-time servicing before a problem occurs.
This type of data cooperation could have huge ramifications for manufacturing inputs, but it could also help meet customer demand for final product outputs.
On a smaller scale, Audi has already implemented automated tracking and processing for shipments to its Ingolstadt plant in Germany. Using sensor data transmitted via smartphone, the plant automatically tracks inbound delivery vehicles from 50 kilometers away. Shipment contents are confirmed with plant logistics without the driver initiating any communications. All check-in processes are carried out and prioritized remotely so that instructions can be delivered automatically to drivers, so all they have to do is drive to a designated delivery point.
Labor And Skills Transfer
Automation is something that's touted much with smart factory development. A major uncertainty has been the role for people.
At a Siemens production facility in Amberg, Germany, people still play a large role in overseeing visual and physical checks throughout the plant. The company embraces a flat hierarchy that encourages employee input — creating demand for more experienced and creative employees. Staff aren't only responsible for ensuring work is performed according to plan. They also implement their own design visions. As Rebecca Rose Jacobs writes for The Independent, "Any employee can initiate a project that requires an investment of less than £8,000, and earns a bonus when he or she suggests changes that are later implemented."
Some might argue that full automation might never have been the goal at all for smart factories. Instead, it's more about empowering decision-makers with the right information. In 2013, Don Busiek, general manager of manufacturing software at GE Intelligent Platforms, presented a human-centric vision for smart factories.
“All of a sudden you can structure your schedule across your plant with more intelligence,” he explains. “You can schedule your shift, your personnel with more intelligence. You can even program the heating in your building with more intelligence.”
“To me, that’s where it’s going,” he says. “It’s not the thousands of pieces of data; you’re slicing it in such a way that it is presented to the right user at the right time based on their role.”
“To me,” he says, “that’s the smart factory of the future.”
Toward People-Centered Automated Design
Automated design is an attractive vision for the future. With the digital advancements of previous decades, we've engendered an exceptionally data-savvy workforce. It's only a matter of time before this knowledge is applied throughout our machine hierarchies. These developments require creativity — with much trialing and de-bugging — to overcome. Keeping smart and creative people at the center of these challenges will be key to progressing beyond them.
About The Author: Brad Done is the vice president at Reliance Foundry Co Ltd. He has more than 25 years experience in manufacturing in North America and overseas